Mød Johanna Wallin
– Produktionsleder for FM Mattssons produkter.
Siden 1800-tallet har FM Mattsson fremstillet blandingsbatterier/brusere i messing - en tradition der betyder meget for Mora og os som virksomhed. Selv i dag støbes de fleste af vores produkter på fabrikken i Östnor, hvor kærligheden til håndværket altid har været en central del af den daglige arbejdsrutine.
Men hvordan ser produktionsprocessen ud, og hvad er de kritiske trin i samlingen af vores produkter? Med hjælp fra Johanna Wallin, produktionsleder i samlingen, vil vi i dette kapitel gennemgå alle faser, som vores blandingsbatterier/brusere gennemgår, før de havner i hænderne på vores kunder.
Hvis du ønsker at komme i kontakt med en af vores dygtige medarbejdere, er du velkommen til at kontakte os her.
Kan du beskrive vores håndværkstradition?
FM Mattsson har en håndværkstradition for at fremstille i messing, der går tilbage til 1800-tallet. Faktisk støbte vi vores første vandhane allerede i 1876. Vi, der arbejder hos FM Mattsson, er meget stolte af vores bæredygtige produkter og at vi stadig har produktionen på vores fabrik. Vi støber stadig næsten alle vores haner, hvilket er helt fantastisk!
Hvor lang tid tager det at producere en blandingsbatteri?
Det tager mellem seks og syv arbejdsdage, og processen kan opdeles i følgende faser:
Kerneproduktion
Den yderst fine kvartssand transporteres fra en beholder uden for fabrikken til en beholder inden i fabrikken. Her blandes sandet med bindemiddel og hærder. Derefter blæses kerneblandingen ind i et formværktøj, hvor den hærder op.
Støberi i støbecelle
Støbecellen er bygget og konstrueret af vores medarbejdere i samarbejde med en lokal automationsvirksomhed. Med over 100 års erfaring inden for støbning ønskede vi at udnytte vores egne idéer om, hvordan man bedst laver en støbeform. Ved hver palle med sandkerner er der et kamera, der overvåger kernenes vinkel og opdager, hvis den ligger skævt. En robot registrerer derefter kameraets data og foretager justeringer baseret på denne information. Støberobotten producerer 100 til 180 blandingsbatterier i timen med støbning i ro. Præcis hvor mange afhænger af produktet. Der er to ovne, der støber skiftevis 20 skud hver, og mens der støbes i den ene, tilføres der ny messing og rengøres i den anden. Støbning i ro betyder, at vi ved skift mellem støbeovnene tilføjer messing og hæver temperaturen. Når messing smelter, bevæger slaggerne sig rundt, og inden man vender tilbage til ovnen, sænkes temperaturen, så slaggerne lægger sig på overfladen. Messingen trykkes op med trykluft (0,3 - 0,5 bar) gennem en pude i ovnen.
Støbning og skæring af stiger
Støbningen og stigerne klippes i stedet for at blive savet af. Klippekraften er cirka 20 tons, og robotten måler støbningen for at sikre, at den er lige ved klipningen.
Kernekstraktion
Rensemaskinen er en sandblæser, der behandler støbegodset med små stålkugler, så sandkernen brydes ned, og sandet løber ud af blanderen.
Skærende bearbejdning & komponentproduktion
Med vores 15 flerspindeldrejebænke producerer vi større serier på op til cirka 10.000-40.000 detaljer. Opsætningstiden er cirka 10-12 timer. Vi producerer omkring 200 forskellige detaljer her - ca. 3,2 millioner detaljer om året.
NC-maskinerne
Med vores 11 enkeltspindelmaskiner fremstiller vi mindre og mere komplekse serier. Opsætningstiden er cirka 1-2 timer. Vi producerer omkring 2000 forskellige detaljer her - ca. 2 millioner detaljer om året.
Vaskemaskine
Til vask af de drejede detaljer bruges en lavalkalisk vaskemaskine, hvor olie, emulsion og spåner skylles væk. Maskinen kan individuelt indstilles for hver kurv med hensyn til rotation eller stilstand, vipning og skylletider. Den har kapacitet til cirka 25 millioner detaljer om året.
Skærende bearbejdning (Hus)
I 2014 automatiserede vi flere af vores maskiner for at forbedre ergonomien og for bedre udnyttelse af maskinerne.
Slibning og polering
Slibningen foregår primært i automatiserede celler, hvor en palle bliver udstyret med et antal blandere, som derefter transporteres ind til en robot, der er programmeret til hver specifikt produkt. Cirka 0,7 mm fjernes her for at fjerne eventuelle uregelmæssigheder på overfladen. Dette er en meget varm proces, i visse tilfælde kan produktet blive op til ca. 500˚C. Vi bruger flere forskellige typer af slibebånd - lige fra enklere, såkaldt sandpapir (silicium) til mere komplekse bånd, der indeholder keramik. Planeringen foregår primært i automatiserede celler, hvor en palle bliver udstyret med et antal blandere til videre transport ind i maskinen, hvor poleringen finder sted. For at opnå det rette resultat bruges to typer voks - en polervoks og en glansvoks.
Overfladebehandlingen
Anlægget påfører både nikkel og krom. Detaljerne placeres på en varebane, som igen hentes af en transportør. Oppe i loftet er der monteret mikrocomputerbaserede optiske afstandsmålere, som ved hjælp af en infrarød stråle reflekteres mod et spejl, der er monteret på transportøren. På den måde kan man måle afstanden præcist til, hvor transportøren befinder sig. Transportøren sænker varebanen ned i forskellige bade i følgende procesforløb:
- Alkalisk affedtning (vask af produkter som sæbe)
- Katodisk affedtning (det samme som ovenfor, men med strøm, hvor 4-10V strøm skubber snavset væk)
- Anodisk affedtning (aktiverer messing med strøm for nikkel, 4-10V)
- Dekapning (filmopløser, miljøvenlig syre, der skylles resterne fra katodisk affedtning væk)
- Nikkel- og forkromning. Detaljerne belægges med 10-20 µ Ni og ca. 0,1-0,3µ Cr
Mellem de forskellige processtadier skylles emnerne i vand. Det brugte skyllevand renses i renseanlægget før udledning. Det tager ca. 75 minutter for emnerne at gennemgå anlægget.
Rør-bøjning
Afkortning/bøjning af komponenter til f.eks. lodning, rør. (Cirka 600 forskellige detaljer om året).
Presning
Her har vi 13 forskellige presse til forskellige typer af fastgørelse og stanseopgaver.
Montering
Under monteringen af termostater, håndvaskbatterier og berøringsfrie armaturer, testes produkterne bl.a. for tæthed med luft og/eller vand, for lukning og for tæthed. Der kontrolleres også temperaturer via et koldt- og brændende varmt vandflow.
Montering og test af berøringsfri vandhane
Vandhane testes for tæthed og den elektroniske funktion prøves.
Test af termostater
Inden testen påbegyndes, kontrolleres det, om det indgående vand har den korrekte temperatur. Det varme vand skal have en temperatur mellem 55 og 65°C, og det koldet vand må ikke være varmere end 15°C. Først kalibreres "låseknappens position" til 39° ± 1°. Når dette er godkendt, kontrolleres koldt- og varmtvandsindstillingerne. Det varme vand skal have mindst 42°, og det koldt vand skal have maksimalt 18°. Maskinen foretager derefter en re-kontrol af "låseknappens position" = 38°C. Til sidst kontrolleres varmtvandsflowet (lækageflowet) ved tab af koldt vand, som ikke må være mere end 0,6 liter pr. minut. Under testprocessen kontrolleres samtidig ydre tæthed, forbindelser, overløb og lignende.
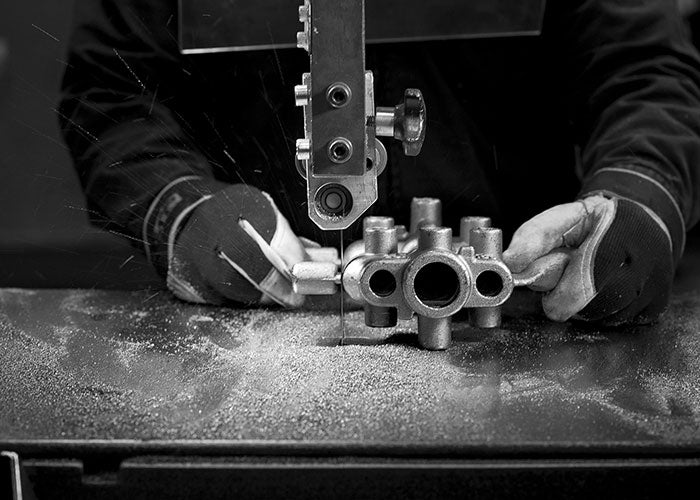
Her kan du se, hvordan fremstillingsprocessen af en vandhane foregår.
Hvor mange personer er involveret?
Det er svært at sige, da vi arbejder med forskellige typer af emner parallelt hele tiden. Gennemsnitligt er der cirka seks til syv personer involveret fra de forskellige afdelinger, for eksempel i en blandingsfacilitet.
Hvad er det vigtigste at tænke på, når man fremstiller et håndvaskarmatur?
At levere den rette kvalitet.
Hvad gør dig mest stolt af at arbejde hos FM Mattsson?
Al den viden, der findes her, og vores flotte bæredygtige produkter.